Plastic Injection Molding
Thermoplastic, thermosetting, and composite materials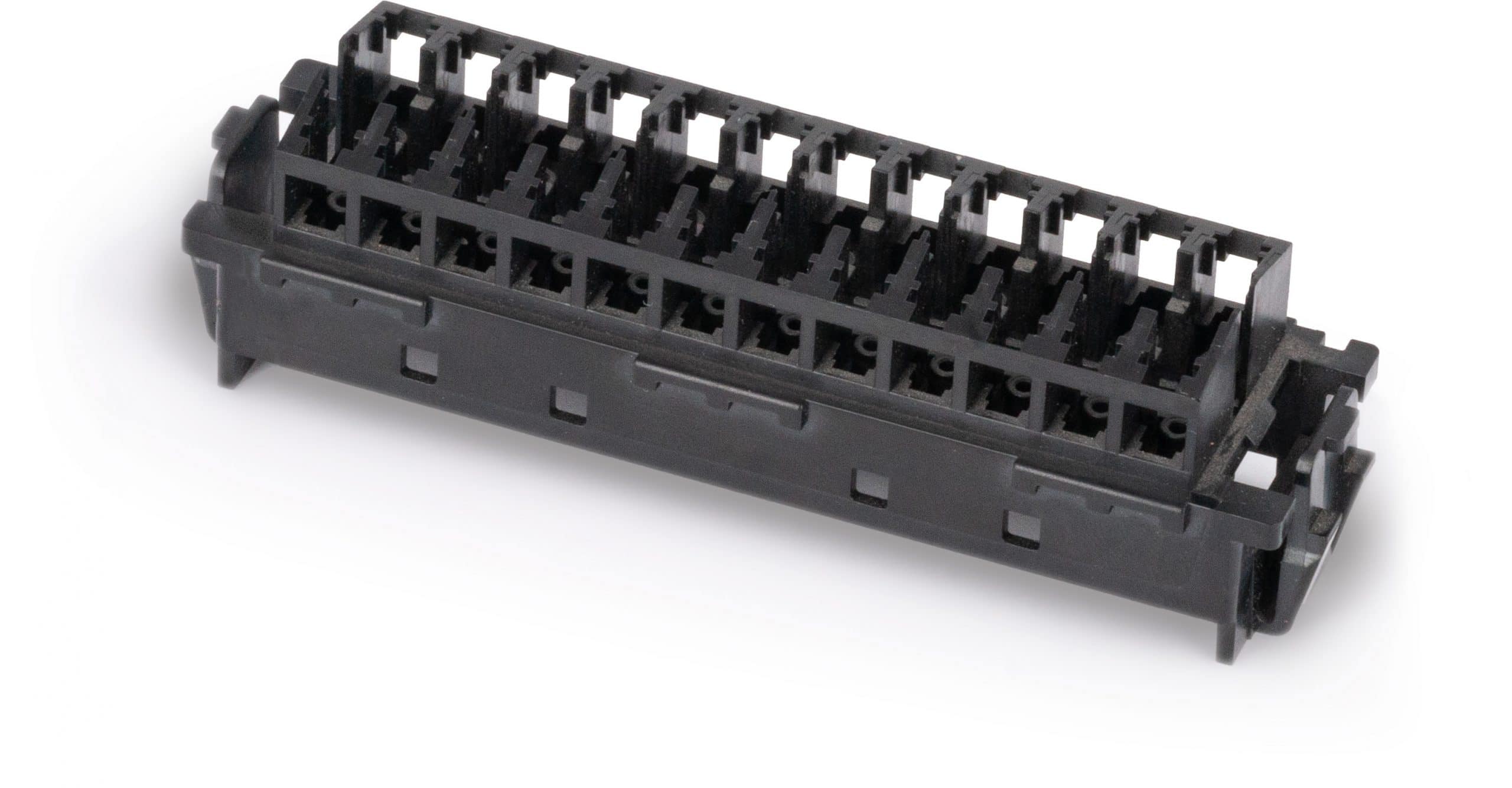
- State-of-the-art manufacturing techniques
- Wide selection of plastics and resins
- Torlon injection molding of all grades
Aztec Plastic specializes in the custom injection molding of highly engineered thermoplastic materials and composites. We have extensive experience in identifying and selecting the best raw materials and resins for our customers’ projects. Whether the need is for special molding material properties or extreme heat or cold requirements for components, Aztec Plastic has the expertise and experience to recommend the best possible solution for your plastic injection molding project.
On the leading edge of innovation for over 50 years, Aztec Plastic specializes in several manufacturing processes sanctioned by ISO 9001:2015 and AS 9100 quality certifications, and we are ITAR Part 122 Registered. In addition to our plastic molding processes, we offer contract manufacturing and assembly services, secondary operations, part product machining, and packaging and kitting.
What we do
- A wide range of plastic injection molding press capabilities ranging from 45 to 500 tons
- ISO 9001:2015 Certified and AS 9100 Aerospace / Defense Certified
- FDA Compliant and TS 16949 Compliant
- White Room manufacturing capabilities
- Automated and semi-automated robotic technology capabilities
- High quality inspection with custom vision systems for manufacturing
- Cell manufacturing capabilities
Injection molding plastic and resin options
Specialty high performance molding capabilities
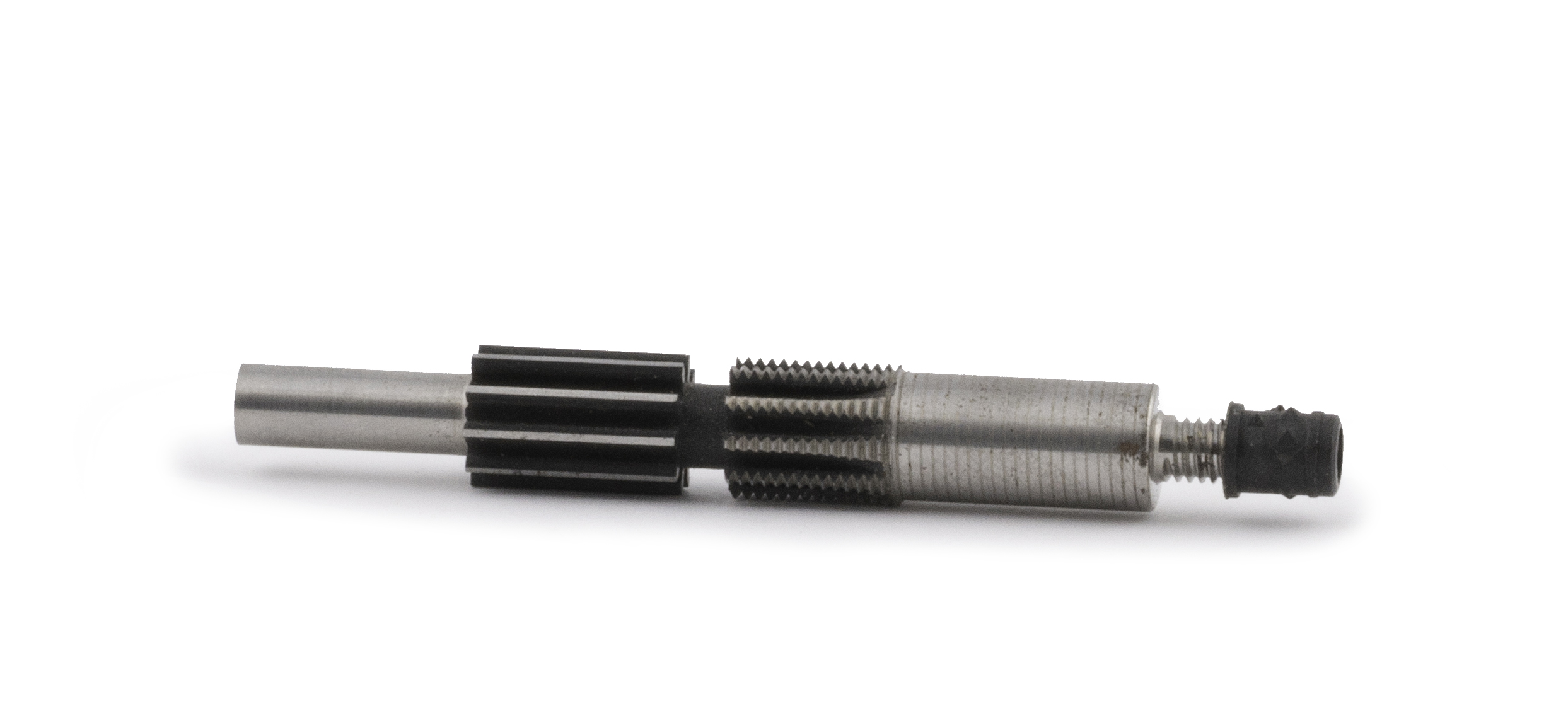
Plastic injection over molding
Over molding is a process that manufactures two or more materials and/or colors within the same product or part. In technical terms, this means multiple materials are injected at two different points or more within the injection mold to create one final part. This process can be utilized across singular or multiple cavities within the injection molding process.
The injection over molding process is ideal for specialty items or products that can eliminate costly secondary processes or assembly. Examples are:
- Gaskets, seals or sealing mechanisms
- Soft touch products
- Functional parts
- Acoustic dampening elements
- Vibration absorbing products
- Decorative or advanced aesthetics
- Permanent descriptions or identifications
- Enclosure of multi-components products
Insert molding
Insert molding lowers the cost of end use products and subassemblies by reducing or eliminating secondary assembly operations and labor costs through the introduction of components into the plastic molding process. This process combines plastic resin with materials like metal stampings, electromechanical parts, machined metal parts, filters, gaskets, and more into a single viable product.
Our custom insert molding services and capabilities include:
- Automated, semi-automated, and manual component insertion
- Post molding secondary operations for electrical testing, machining, bonding, etc.
- Post manufacturing quality inspection capabilities
- Design of manufacturability for multi-components
- Custom designed tooling and fixturing
- Advanced materials selection
Decorative and cosmetic molding
Decorative molding has been a growing industry requirement within the plastics industry for several years, and Aztec Plastic has been at the forefront of this process. It is used when a product requires extremely high aesthetics or visually appealing external features. The decorative features of a product may include visual aesthetics, special textures, lens quality requirements, scratch free surfaces, and unique colors, materials, or packaging.
Aztec Plastics has over 50 years of experience with the following processes which are critical to producing excellent quality decorative molding:
- Advanced decorative applications
- Specialized material selections
- High end manufacturing processes
- Two shot over molding processes
- Color printing
- Pad printing
- Laser etching
- Texturing
- Assembly
- Specialized packaging and kitting solutions
- Labeling
In mold decorating
In mold decorating (IMD) or in mold labeling is a highly unique and specialized method of injection molding which introduces a label or applique into the injection molding manufacturing process. This label or applique can be decorative or instructional and becomes a semi-permanent, imbedded component of the molded object.
The in mold decoration process injects molten material or plastic resin into a specially designed tool in which the label or applique becomes an integral part or attribute of the plastic molded product. This special injection molding process provides increased durability, strength, creative design, decorative, and cosmetic options to the finished goods and products.
Aztec Plastic’s in mold decorating services offer several advantages:
- Consultative interaction for manufacturability
- Specialty material selection assistance for resins and applique
- Automated introduction, placement, and positioning of the applique or label
- Manual and semi-automated options
- Early involvement engineering for custom applique or label design
Molded in color and multi shot molding
Molded in color and multi shot molding refer to molding plastic parts with two or more colors or materials in a single injection molding operation and machining cycle. Using this plastic injection molding method, Aztec Plastic can give your product a high quality, long lasting color and finish. The advantages of molded in color and multi shot molding are coloring that can withstand harsh environments, no paint scratching or peeling, no secondary painting, with faster and lower cost part production.
Aztec Plastic can use molded in color and multi shot molding to create a wide variety of plastic products, including:
- Body panels, fenders, and housings for the automotive industry
- Recreational and marine vehicle components
- Plastic parts for agricultural equipment
- Industrial and consumer appliances
- Lawn and garden equipment components
In-house tool services
Our team knows the importance of mold durability. We are proud to offer in-house mold repair and service to keep production smooth and exemplary. Every mold is different with varying components. When it comes to repair, we focus on:
- Alignment
- Cavity/Core
- Ejector Pins
- Parting Lines
- Runner/Gate
- Vent/Vent Dumps
Rest assured, we go above and beyond with every inspection, cleaning, pre and post installation, and repair service. By providing in-house expertise, we cut delay time and ensure the mold is at the highest quality for unique part specifications.
The Aztec Advantage
At Aztec Plastic, we are a flexible asset and partner to our customers. Whether it is high production, high mix low production, developmental or conceptual, we adapt our business to best support our customers’ needs and concerns.
Our mission is to be the highest quality driven organization that utilizes the latest cutting edge manufacturing technologies striving towards continuous improvement. Our goal ultimately is to be the benchmark for our customers’ suppliers.
Hear from our clients
“They are a very high end molder… can do complicated, high temp specialty engineering products. They do a lot of things other molders will not do.” – Buyer, Aerospace Company
“They’re not scared to take on the hard jobs. Always willing to go the extra bid and willing to stay no if they can’t do it… they are willing to be a better supplier…” – Buyer, Automotive Company