Plastic Centerless and Cylindrical Grinding
High quality plastic machining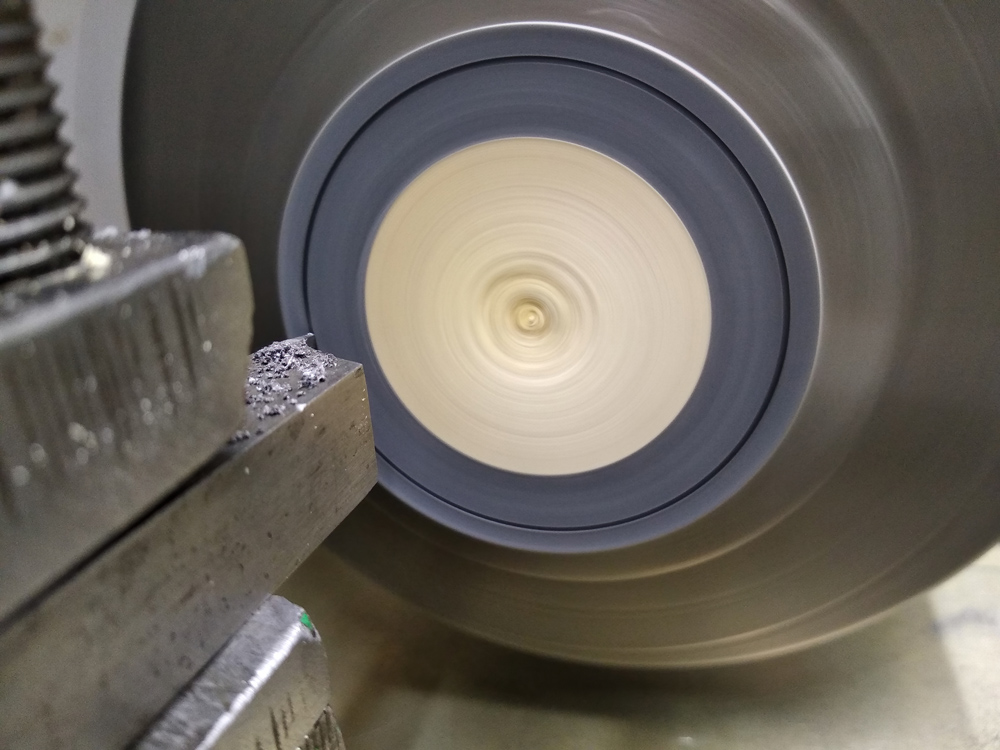
- Create precise plastic products
- Capabilities for large production runs
- Contract manufacturing available
Centerless plastic grinding
Centerless plastic grinding is a machining process that removes material from the outside of a cylindrical item through the method of abrasive cutting in order to achieve the desired size, smoothness, and roundness. The concept is relatively simple: the workpiece is fed between two wheels rotating at different speeds, with the grinding wheel rotating at a speed that applies a downward force to the workpiece. The regulating wheel (or moving wheel) applies lateral force to the workpiece and controls the rotational speed.
These wheels can have a variety of grain types and grit sizes, such as polycrystalline diamond or cubic boron nitride. The various grit sizes on the wheel produce different diameters, widths, and thicknesses, depending on your required specifications.
Aztec Plastic offers both through feed and infeed centerless grinding. The through feed method is used for parts with consistent roundness across their length, while infeed is used for cylindrical parts with complex shapes or notches.
Benefits of centerless grinding
- Centerless grinding allows a high volume of parts to be processed at once, because it works at high speeds.
- Centerless grinding can be used in a wide variety of industries, including aerospace, automotive, military, medical and more.
- CNC programmable controls increase the efficiency of the grinding process by decreasing the time it takes to set up between jobs. Robotics advancements are also paving the way for automatic loading and unloading of workpieces, reducing labor costs even further.
Plastic cylindrical grinding
Cylindrical grinding is another plastic forming process that we use to grind plastics to a particular shape. Aztec Plastic specializes in cylindrical grinding of thermoplastic, thermosetting, and composite material.
Cylindrical grinding works by clamping a cylindrical object between two centers or a chuck, and then grinding with a wheel at a desired diameter. With cylindrical grinding both the object and the grinding wheel are constantly rotating. This method of grinding does not leave a spiral or groove pattern, creating a smooth finish for plastic parts. Using this plastic grinding process, we create a wide range of products, including gears, pins, pistons, tubes, valves, spools, sleeves, shafts, hydraulic components, and many more.
Benefits of cylindrical grinding
- Achieve extremely close tolerances and precise round angles
- Costs less compared to other plastic grinding processes
- Excellent finish quality on all cylindrical ground projects
Benefits of cylindrical grinding
- ¼” to 4” diameter by 10” long sizes
- Roundness
- Hydraulic/Pneumatic methods