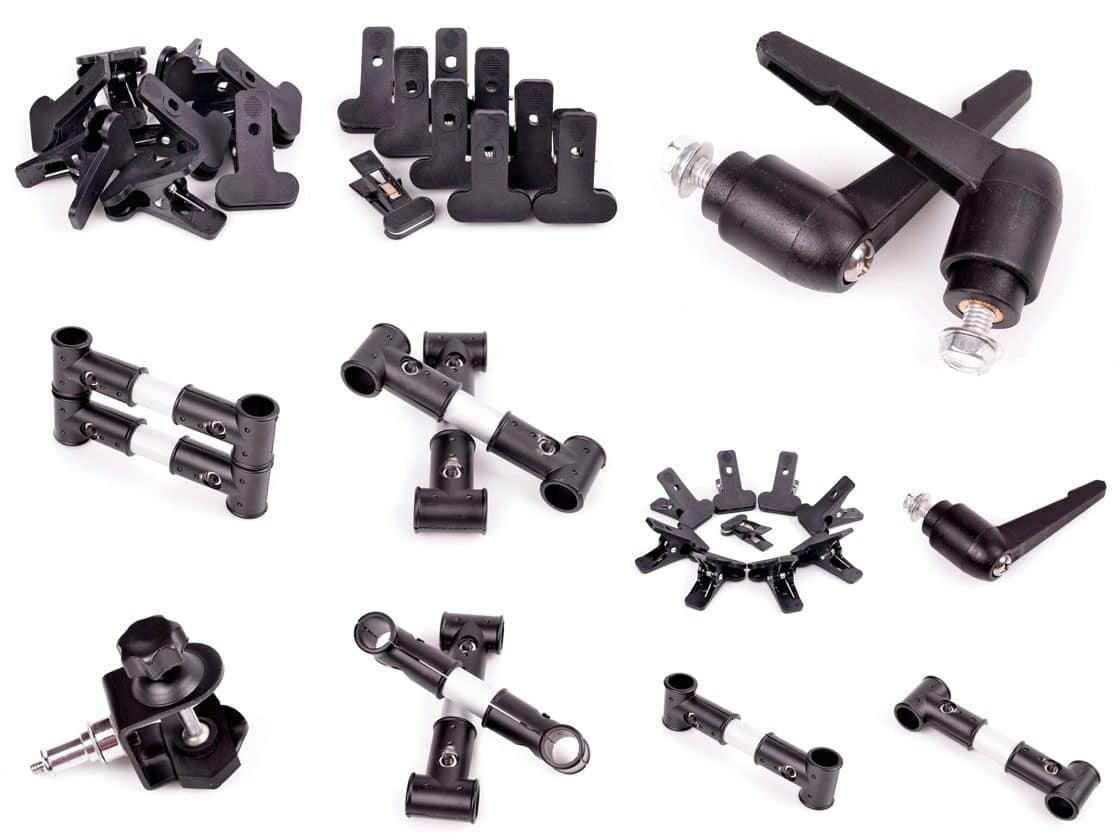
How Plastic Parts Are Changing the Automotive Industry
The use of plastics in the automotive industry is on the rise. According to the American Chemistry Council, more than 5.7 billion pounds of plastics are employed for automobile production annually. Why? Because high performance plastics have environmental and economic advantages. In fact, almost 50% of the volume of a new light vehicle is made of plastic, but plastic makes up less than 10% of a new light vehicle’s weight.
At Aztec Plastic, we create automotive components using Torlon, PEEK, Ryton, Ultem, and other types of industrial plastics.
Plastics car parts reduce emissions
Cars with plastic components are lighter and more fuel efficient, reducing greenhouse gas emissions. When a vehicle’s weight decreases by 10%, its fuel economy increases by 6% to 8%. Other benefits include increased recyclability and flexibility, plus minimal corrosion. Plastic automotive components also reduce manufacturing and assembly times and repairs, contributing to reducing overall resources and energy used by the industry.
Plastic injection molding for discontinued automotive parts
A new development for plastics in the automotive industry is in the manufacturing of parts for out of production vehicles. Once car models are discontinued, manufacturers still need to provide replacement parts for those models over an extended period of time. Producing and storing components for models that have been scraped, upgraded, or overhauled can be very expensive, challenging, and, sometimes, unsustainable.
Torlon in the automotive industry
Torlon offers numerous benefits that make it perfect for vehicles. It has a high temperature resistance, and it can be extruded and injection molded with precision. As a result Torlon can be easily shaped into custom parts with very tight tolerances and exact specifications, ideal for automotive parts. Its wear and strength properties make it perfect for use in powertrains, cooling and heating systems, engine management systems, oil and fuel circuits, and transmission parts.
Torlon auto parts are:
Quiet – Torlon parts do not transmit noise and vibration like metal components do.
Wear resistant – Torlon resists chemicals, organic compounds, and friction without external lubrication.
Compatible with auto engine fluids – Torlon stays inert and does not react when exposed to all types of automotive fluids.
Lightweight – Torlon plastic is half the weight of aluminum.
PEEK in the automotive industry
Similar to Torlon, PEEK can be injection molded and machined to create highly precise automotive components. It is exceptionally strong and temperature resistant, making it an ideal choice for replacing a wide range of metal parts. PEEK is widely used to create car engine components like electrical sensors, clutch parts, gears, braking systems, transmission components, bushings, seals, and more.
Properties of PEEK that make it ideal for the automotive industry include:
High strength – Even when it is used at 500° Fahrenheit for 5,000 hours, PEEK maintains nearly the same strength as it has in its initial state, plus excellent thermal stability.
Wear resistant – PEEK resists thermal, chemical, organic, radiation, and aqueous degradation. It also is very hard to prevent cracking.
Low emission – When exposed to fire, PEEK produces low levels of smoke and toxic gas emissions.
ULTEM in the automotive industry
ULTEM is a thermoplastic that can operate in environments with very high temperatures. Its high tensile strength and heat and chemical resistance make it one of the best candidates for plastic metal replacement. It also has excellent electrical properties, with one of the highest dielectric strengths of any industrial plastic. For this reason, ULTEM is commonly used for high voltage electrical insulation applications.
Examples of ULTEM auto parts include:
Drive train components
Braking system components
Electrohydraulic control valves
Electrical insulators
Transmission parts
And more!
Ryton in the automotive industry
Ryton automotive components can withstand high temperatures, large amounts of mechanical stress, and corrosive automotive fluids, especially OAT and long life engine coolants. It is widely used to manufacture under hood parts, brake system components, car computers, air ventilation ducts, and other high tech parts that are exposed to high heat environments.
The benefits of Ryton automotive parts include:
Precision – Ryton can be injection molded and machined to exact specifications.
Lightweight – By replacing metal, Ryton makes components lighter and less expensive, leading to lower manufacturing costs and greater fuel efficiency.
Heat resistance – With engines becoming more compact, “hot spots” can often exceed the thermal capabilities of metal and rubber, but Ryton can take the heat.
The key to plastic sustainability is recycling
Plastics are extremely versatile due to their ability to be molded, formed, and machined with precision, repeatability, and cost effectiveness. Industrial plastics are used to protect us from moving parts, electricity, germs, oxidation, heat, cold, and more. Despite producing so much good, in many industries in addition to automotive, plastic often is associated with negative environmental impacts. But because of the immense benefits plastics provide, the key to moving forward sustainably is building a better recycling infrastructure with progressive programs for reuse and recovery.
With technological advancements, the amount of plastic used in the auto industry will increase. Not only do new additional luxury features often require plastic parts, but plastics are replacing steel due to their unique benefits. If the proper measures are taken, industrial plastics and plastic injection molding have a bright future in the auto industry!