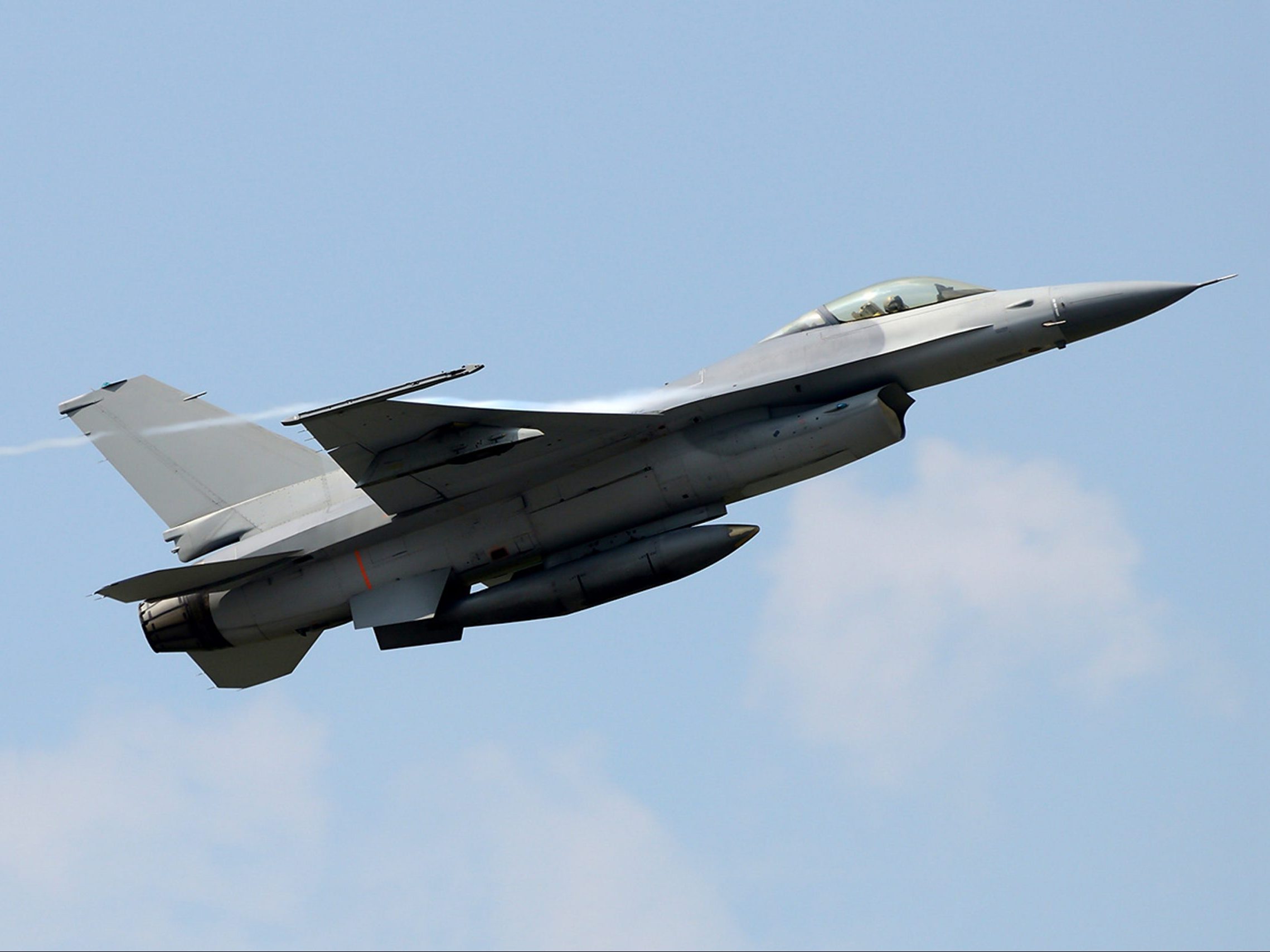
How Torlon Is Used in the Aerospace Industry
Plastics are found in commercial planes, military aircraft, and even satellites. A wide range of parts in the defense industry such as aerospace are made from plastics. Engineers first experimented with vinyl materials to see whether rubber parts, such as fuel tank linings, could be replaced by plastic ones, then progressed to substituting a wide variety of glass and metal components with plastic ones.
Benefits of plastic in airplanes
Plastics offer many advantages over other types of materials. For example, plastics reduce manufacturing and operating costs and, in general, can be manufactured more economically than glass and metal. Plastics are also much lighter compared to many commonly used materials in aircraft components. For instance, plastics are about 50% lighter than aluminum. Because heavier planes, like those made of aluminum, require more fuel to move, lighter planes, like those with plastic components, reduce costs, saving both money and energy.
Additionally, plastics stand up in harsh conditions better than other materials. Unlike metals, they are resistant to corrosion and more impact resistant than glass. Plastics also provide electrical insulation, with some having almost zero conductivity.
Why use Torlon in the aerospace industry?
Torlon is one of the most commonly used plastics in aircraft and their components. It is the highest performing, melt processable thermoplastic on the market. Torlon’s exceptional mechanical strength makes it appropriate for applications in severe situations, including temperatures up to 500 °F. In addition, it has good creep, thermal, chemical and flame resistance as well as low thermal expansion, making it ideal for metal replacement in tough or extreme situations.
How Torlon is used in aerospace and defense
Torlon has the unique capability to withstand both hot and cold extreme environments. Along with being lightweight and strong, Torlon has many properties that make it ideal for aircraft components.
Torlon aerostructure – At Aztec Plastic, we use Torlon to create aircraft wings, doors, pipes, leads, and cable ducts.
Torlon aircraft components – Torlon is widely used to manufacture aircraft fasteners, bearings, bushings, refueling and fuel systems.
Torlon control and propulsion systems – We use Torlon to manufacture landing gear, aircraft propulsion system components.
Torlon for aircraft cabin interiors – Aircraft seating, cabin lighting, and drinking water systems all typically include Torlon components.
Torlon thermal isolators – Torlon is used to insulate hydraulic lines that run through fuel tanks to protect them from heat and electrical energy, greatly reducing aircraft weight.
Torlon engine shrouds – Engine shrouds made from Torlon retain their mechanical properties at high temperatures, resist deformation, and reduce noise and vibrations.
Torlon clip nuts – Non-corrosive Torlon clip nuts achieve aircraft weight reductions over metal, allowing for large gains in fuel efficiency.
Additional uses of Torlon aircraft components include sector gears, bushings, screws, and air connections. Like the examples listed above, the benefit of using Torlon lies primarily in its high and low temperature resistance, high strength, and lightweight properties. Additionally, Torlon can be injection molded or 3D printed into nearly any shape or configuration at a low cost, helping manufacturers reduce costs and production timelines.
For these reasons, Torlon and similar plastics are quickly replacing both glass and metal throughout the aerospace and defense industries.