Plastic Injection Molding for Off Highway and Off Road Vehicles
Handle the toughest environments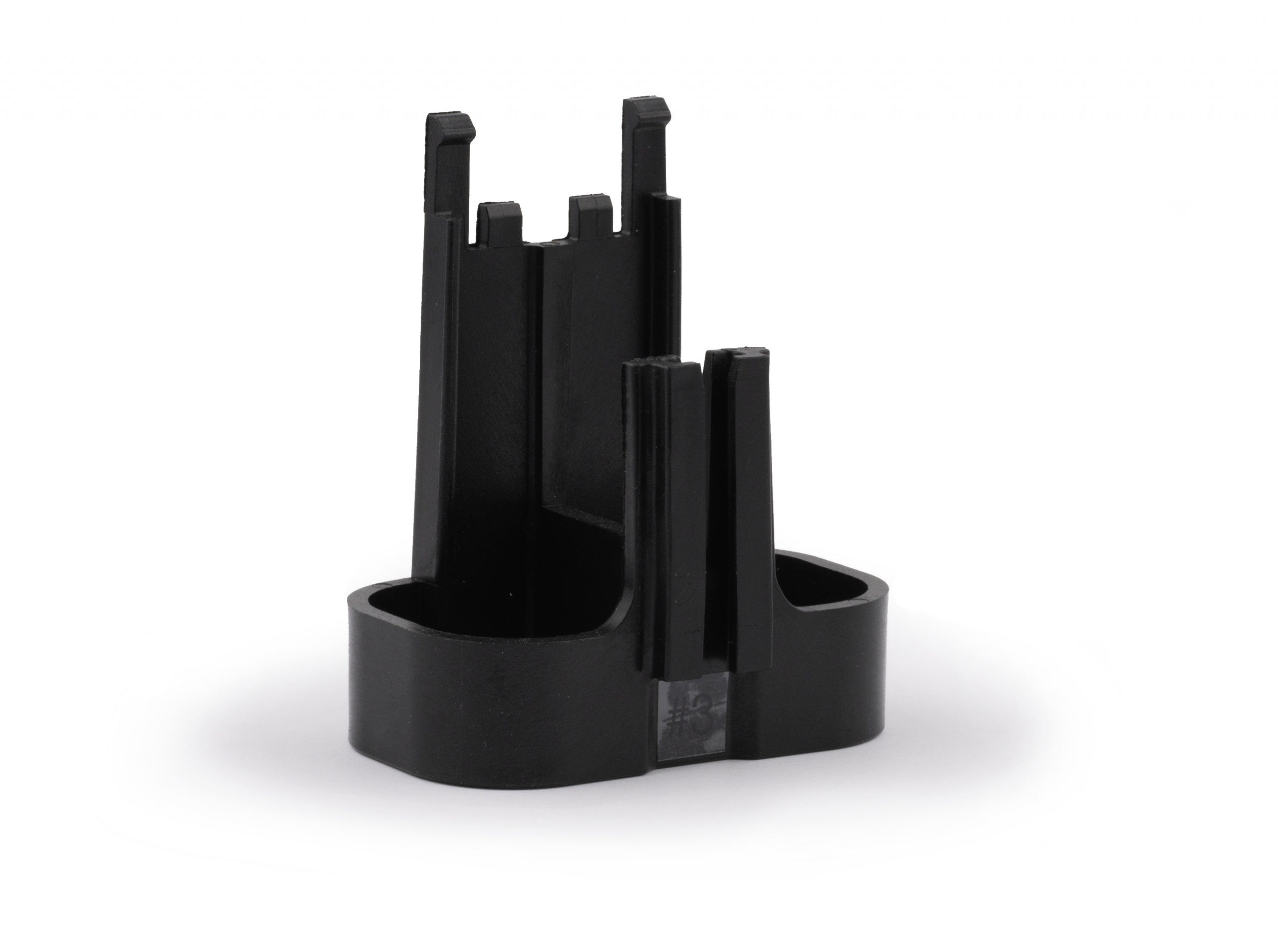
- High strength plastic components resist wear from weather and heat
- Suitable for a wide variety of precision components
- Production runs are completed quickly
Why use plastic in off highway vehicles
Plastic has numerous advantages over metal and other more traditional materials. First, they are highly resistant to heat and corrosion, not suffering from rust and other forms of breaking down that are common with metals. They also withstand weather and the elements and have a much longer service life. For off road vehicles and equipment that operate in the rain, mud, snow, and sunlight, thermoplastics and plastic resins are the best choice for high strength, long lasting components.
In addition to being resistant to chemicals, heat, and weather, plastic components also have a much shorter production time than their metal counterparts. Plastic Thermoforming is far less labor intensive than metal manufacturing. Plus, plastic injection molding and 3D printing reduce costs, because they require less energy and labor in manufacturing processes compared to time consuming metal fabrication methods.
Uses of plastic in off road equipment
Plastics are used in many different parts for both recreational and commercial off road machines.
- Plastic components for off highway vehicles – Plastic injection molding is used to create high quality gears, wear pads, sheaves, housings, plug seals, nuts with gaskets, poppets, electrical components, and more in off highway equipment.
- Plastic components for snow mobiles and ATVs – In addition to gears, seals, electrical, and other engine parts, plastic injection molding for recreational vehicles is also used to create seats, seat backs, roofs, storage boxes, snowplow attachments, and more.
Plastics we work with for off road equipment
Aztec Plastic applies a range of plastics and resins for recreational and off highway vehicles, depending on what’s best for the specific application. Our plastic injection molding process uses polyamides, acrylonitrile butadiene styrene, polyesters, polycarbonates, acetals, thermoplastic elastomers, thermoplastic polyurethane, polystyrene, polyamide imide, polyethylene, polypropylene, and more. Injection molding, 3D printing, and secondary machining allow us to create highly precise components that meet the tightest tolerances. Plus, we also create 3D prototypes, so you can be sure every part or component meets your requirements before starting the full production run.
From 1 piece to 10+ million pieces, Aztec has you covered
- Prototype stage and all you need is a couple of parts
- Low volume projects, 50-5,000 pieces
- Multiple programs, but low volume
- High volume contract manufacturing project with millions of parts needed annually
Is Aztec a good fit for your company?
- Use off-road vehicles and equipment
- High volume solutions
- Work in diverse environments
- Reduce labor and manufacturing costs
- Require high quality components