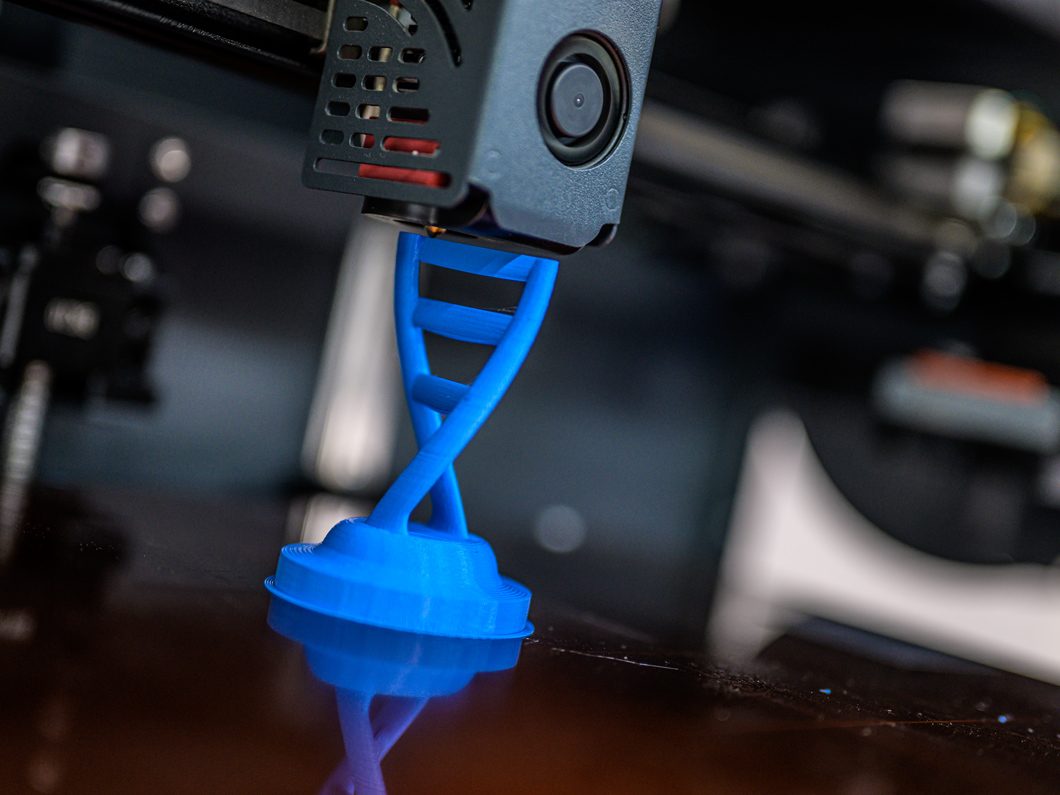
Our Plastic 3D Printing Methods
We manufacture high quality, cost effective plastic products
- We use a wide range of 3D printers and methods
- Highly precise, durable plastic parts and components
Plastic 3D printing reduces production time and manufactures products at a lower cost than other methods. At Aztec Plastic, we use 3D printing, also known as additive manufacturing, to print casting molds, create prototype parts, and manufacture components like heat exchangers, that are traditionally difficult and expensive to make.
In order to find out how 3D printing can apply to your work and increase work efficiency, you first need to understand the various options that are available. Below are the nine 3D printing methods we use at Aztec Plastic.
Types of 3D printing
Stereolithography (SLA)
Stereolithography 3D printing uses an ultraviolet laser beam, which solidifies a layer of liquid resin through a method called photopolymerization. SLA builds an object from the bottom up, layer by layer. After the object is made, it is treated with a solvent bath and also often put in a UV oven.
Pros
- Efficient prototyping method
- Accuracy and precision with fine details
- Economical option for aerospace and automotive industries
- Can be used with many different types of resin
Cons
- May be more expensive than other printers, such as FDM printers
Common Uses of Stereolithography: Prototypes, objects that require fine details and smooth surfaces, and castable molds in the jewelry and cosmetic dentistry industries
Digital Light Processing (DLP)
Digital light processing 3D printing uses traditional light sources, such as arc lamps, to solidify photopolymers. All layers are exposed to the light source at once instead of layer by layer. With the DLP methodology, objects can be produced faster than with SLA.
Pros
- Strength of the 3D objects made
- High resolution objects
- Economical—usually less expensive than SLA printers
- Fast printing speed
Cons
- DLP printers are larger than SLA printers
- The process may be more expensive than FDM printing due to the cost of photosensitive resin
Common uses of Digital Light Processing: Prototypes, injection molding patterns, metal casting applications
Fused Deposition Modeling (FDM)
FDM printers use thermoplastic materials like Torlon, polyethylene, polyurethane, and many others. After creating a 3D model using CAD software, the plastic model is sliced into different layers by a software called QuickSlice. Then, the printer builds the object from the bottom up, one layer at a time.
Pros
- Accuracy
- Great strength to weight ratio
- Highly cost effective
- Easy to use, controlled by computer software
Cons
- Unable to produce very large objects
- There are restrictions on the materials that can be used
Common uses for Fused Deposition Modeling: Prototypes, manufacturing aids, concept models (especially in mechanical engineering) for small businesses and in education
Selective Laser Sintering (SLS)
The Selective Laser Sintering 3D printing method uses high powered CO2 lasers to sinter powdered materials. Powdered metal materials, ceramics, glass, white nylon powder, steel, and silver can all be used. Since un-sintered powder acts as protection, SLS printing does not require additional support structures.
Pros
- Can utilize a wide range of materials
- Precision
- Durable 3D objects
Cons
- Expensive due to the high powered lasers that are used
Common uses Selective Laser Sintering: Prototypes, end use parts, iterative testing, form and fit testing
Selective Laser Melting (SLM)
In SLM 3D printing, a high powered laser beam is used to melt and fuse metallic powders and convert them into solid 3D objects. Materials such as cobalt chrome, aluminum, stainless steel, and titanium are utilized. SLM printing does not require extra support structures, since the excess powder works as protection.
Pros
- Very strong and durable 3D objects
- Do not need additional post processing
Cons
- More costly than some other printers
- A little weaker than forged or milled 3D parts
Common Uses of Selective Laser Melting: Parts that have more complicated structures, geometries and thin walls; objects that have internal voids; energy, aerospace, medical orthopedics industries; universities
Electronic Beam Melting (EBM)
Similar to SLM, EBM 3D printing also involves layers of powders being melted to form a three dimensional object. However, unlike SLM, Electric Beam Melting uses a strong electron beam in a high vacuum. The beam is controlled by a computer and uses high temperatures to melt metallic powders such as titanium.
Pros
- Creates dense and strong 3D objects
- Produce objects with complex structures and geometries
Cons
- The EBM process is often slower than other 3D printing methods
- Costly; it can be technically demanding to create a vacuum chamber
Common Uses of Electronic Beam Melting: Metal parts, aerospace parts, medical implants, prototypes, support parts, small series parts
Laminated Object Manufacturing (LOM)
Laminated Object Manufacturing is cost effective, as it uses relatively inexpensive materials, such as paper and plastic. These paper and plastic laminates are fused under both heat and pressure. Then, a computer controlled laser or blade shapes the materials. LOM 3D printing creates objects one layer at a time.
Pros
- One of the fastest 3D printing methods
- Highly affordable 3D printers and low cost materials
- Can create relatively large objects
- Ability to produce full color objects
Cons
- Dimensions not as accurate as SLA or SLS printing
Common Uses of Laminated Object Manufacturing: Often used by product developers, artists and architects
Binder Jetting (BJ)
Binder Jetting 3D printing, also referred to as “powder bed printing,” “inkjet 3D printing”, and “drop-on-powder printing”, uses a bonding agent as an adhesive to put power based materials together. Some popular BJ printing materials include plastics, sand, ceramics, and metals.
Pros
- Print objects in full color by adding color pigments
Cons
- Lower resolution than other 3D printing methods
- Objects not as robust
Common Uses of Binder Jetting: Rapid prototyping, short-run manufacturing; Aerospace, automotive, medical industries
Material Jetting (MJ)
Material Jetting printing, also called “wax casting”, is a technique that has been used by jewelry makers for centuries. Today, Aztec Plastic uses 3D printers that make wax casting an automated process.
Pros
- High resolution
- Accuracy
- Great surface finishes
- Can create objects with complex geometries
Cons
- Castable wax is fragile and can also deform over time
- A restricted number of wax like materials that can be used for MJ printing
- Relatively slow build process
Common Uses of Material Jetting: High resolution parts for medical and dental industries and jewelry makers